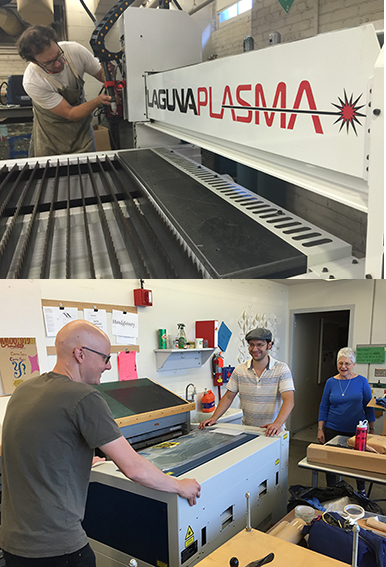
The Department of Art and Art History, with additional support from the Hixson-Lied College of Fine and Performing Arts and private donors, has invested nearly $150,000 for new state-of-the-art equipment installed this summer.
The department has purchased a three-axis CNC (computer numeric control) router, a CNC plasma cutter, six 3-D printers and two laser cutters. One laser cutter was installed in the printmaking studio; the other equipment is in the department’s fabrication and sculpture spaces in the lower level of Richards Hall.
“These are capabilities that we have wanted,” said Pete Pinnell, professor and chair of the Department of Art and Art History. “We want our students to have access to the latest tools and capabilities, both for their own creative potential and so they know what’s out there when they get out into the real world. It’s exciting for what we can do with it, and what potential it opens for our students down the road.”
The CNC router is a computer-controlled cutting machine that cuts hard materials, such as wood, aluminum, steel, plastics and foam.
The CNC plasma cutter uses a computer to create shapes to be cut and to control the cutting machine. The resulting shapes are smoother than what is possible with a bandsaw and can include intricate curves, inside cuts and sharp corners. It was purchased with support from the James C. and Rhonda Seacest Program Excellence Fund.
The laser cutters use a laser beam to etch into an organic material, such as wood or plastic.
“It can be used to make a finished object or parts of an object, or it can be a step toward a finished object, such as creating a ceramic mold,” Pinnell said.
Finally, the 3-D printers act like an inkjet printer, but the printer raises as it prints so it can create objects in three dimensions from a digital file.
“3-D printing has an additive process. It builds and builds and builds,” Pinnell said. “The other machines are a subtractive process. They cut or grind or burn away parts of something.”
Pinnell said computers are changing the way people create art.
“Most of us tend to associate the computer with design and with commercial work, except in photography,” he said. “But what’s happening now is that’s just not the case. People are using the computer as a creative tool in all fields of visual art. This just gives us other abilities to translate from a computer design into an object.”
The equipment is part of the re-branding of the traditional “wood shop” into a fabrication space, which included the hiring last year of Matt Bukrey as the Art Fabrication Space Manager.
“The name ‘wood shop,’ especially for students, has the implication of being a male domain,” Pinnell said. “We wanted to signal that this was for all students and for all faculty to work. Creativity is not linked to gender in any way. But besides that, we knew we were going to be moving in new directions that went beyond traditional woodworking tools.”
Pinnell plans to purchase an industrial-sized sewing machine this year, too.
“We always have students doing things with cloth, and they wear out their own sewing machines trying to sew heavy-duty cloth,” he said. “The whole idea of fabrication shows that we go way beyond just the traditional table saws, chop saws and chisels.”
Faculty will be trained on the new equipment so that they can teach students how to use it.
“The interesting thing about this technology is that no one on the faculty used this in school,” Pinnell said. “These are all capabilities that have come about since we were in college. All of us have followed the rise of this. We’ve all seen it, and some of us have used it and used the software that drives it, but it will be a new adventure.”
Cather Professor of Art Karen Kunc said she is excited to have a new laser cutter in printmaking and will be working with the advanced students to integrate the new technological tool into their plate-making experiences for fine art printmaking.
“This is an ideal way to investigate the qualities and differences of ‘hand’ work and the ‘mediated’ mark that can be cut with the laser,” Kunc said. “I expect we all will face a big learning curve with the new programs and equipment, and how to apply it in ways that augment our other approaches. So adapting—and challenging—the latest technologies is a great opportunity and part of the continuum of print media. I can think of ideas for my own work that I want to try also—intricately carved blocks or detailed engraved plates—that can offer some additional enrichment to my print practice.”
Nearly every area of the department will likely use this new technology.
“There is no area of the department that will not make use of these, except maybe art history. But on the art and design side, everyone will use this equipment,” Pinnell said.