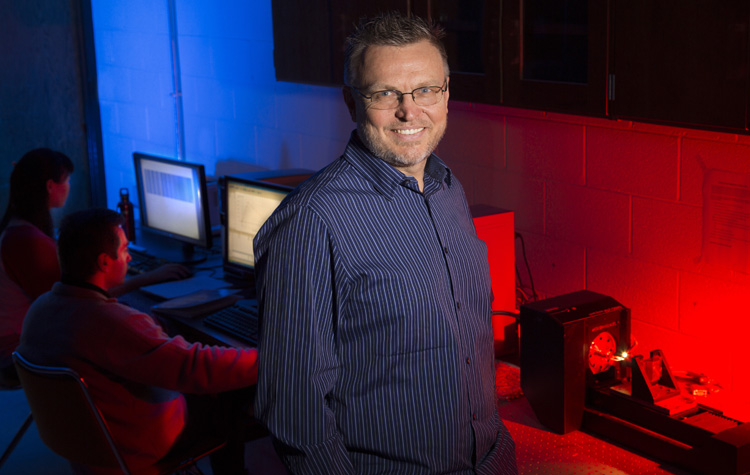
UNL materials engineers have developed a structural nanofiber that is both strong and tough, a discovery that could transform everything from airplanes and bridges to body armor and bicycles. Their findings are featured on the cover of this week’s April issue of the American Chemical Society’s journal, ACS Nano.
“Whatever is made of composites can benefit from our nanofibers,” said the team’s leader, Yuris Dzenis, McBroom Professor of Mechanical and Materials Engineering and a member of UNL’s Nebraska Center for Materials and Nanoscience.
“Our discovery adds a new material class to the very select current family of materials with demonstrated simultaneously high strength and toughness.”
In structural materials, conventional wisdom holds that strength comes at the expense of toughness. Strength refers to a material’s ability to carry a load. A material’s toughness is the amount of energy needed to break it; so the more a material dents, or deforms in some way, the less likely it is to break. A ceramic plate, for example, can carry dinner to the table, but shatters if dropped, because it lacks toughness. A rubber ball, on the other hand, is easily squished out of shape, but doesn’t break because it’s tough, not strong. Typically, strength and toughness are mutually exclusive.
Dzenis and colleagues developed an exceptionally thin polyacrilonitrile nanofiber, a type of synthetic polymer related to acrylic, using a technique called electrospinning. The process involves applying high voltage to a polymer solution until a small jet of liquid ejects, resulting in a continuous length of nanofiber.
They discovered that by making the nanofiber thinner than had been done before, it became not only stronger, as was expected, but also tougher.
Dzenis suggests that toughness comes from their nanofibers’ low crystallinity. In other words, it has many areas that are structurally unorganized. These amorphous regions allow the molecular chains to slip around more, giving them the ability to absorb more energy.
Most advanced fibers have fewer amorphous regions, so they break relatively easily. In an airplane, which uses many composite materials, an abrupt break could cause a catastrophic crash. To compensate, engineers use more material, which makes airplanes, and other products, heavier.
“If structural materials were tougher, one could make products more lightweight and still be very safe,” Dzenis said.
Body armor, such as bulletproof vests, also requires a material that’s both strong and tough. “To stop the bullet, you need the material to be able to absorb energy before failure, and that’s what our nanofibers will do,” he said.
Dzenis’ co-authors are mechanical and materials engineering colleagues Dimitry Papkov, Yan Zou, Mohammad Nahid Andalib and Alexander Goponenko in UNL’s Department of Mechanical and Materials Engineering, and Stephen Z.D. Cheng of the University of Akron, Ohio.
This research was funded by the National Science Foundation, the Air Force Office of Scientific Research and a U.S. Army Research Office Multidisciplinary University Research Initiative grant.