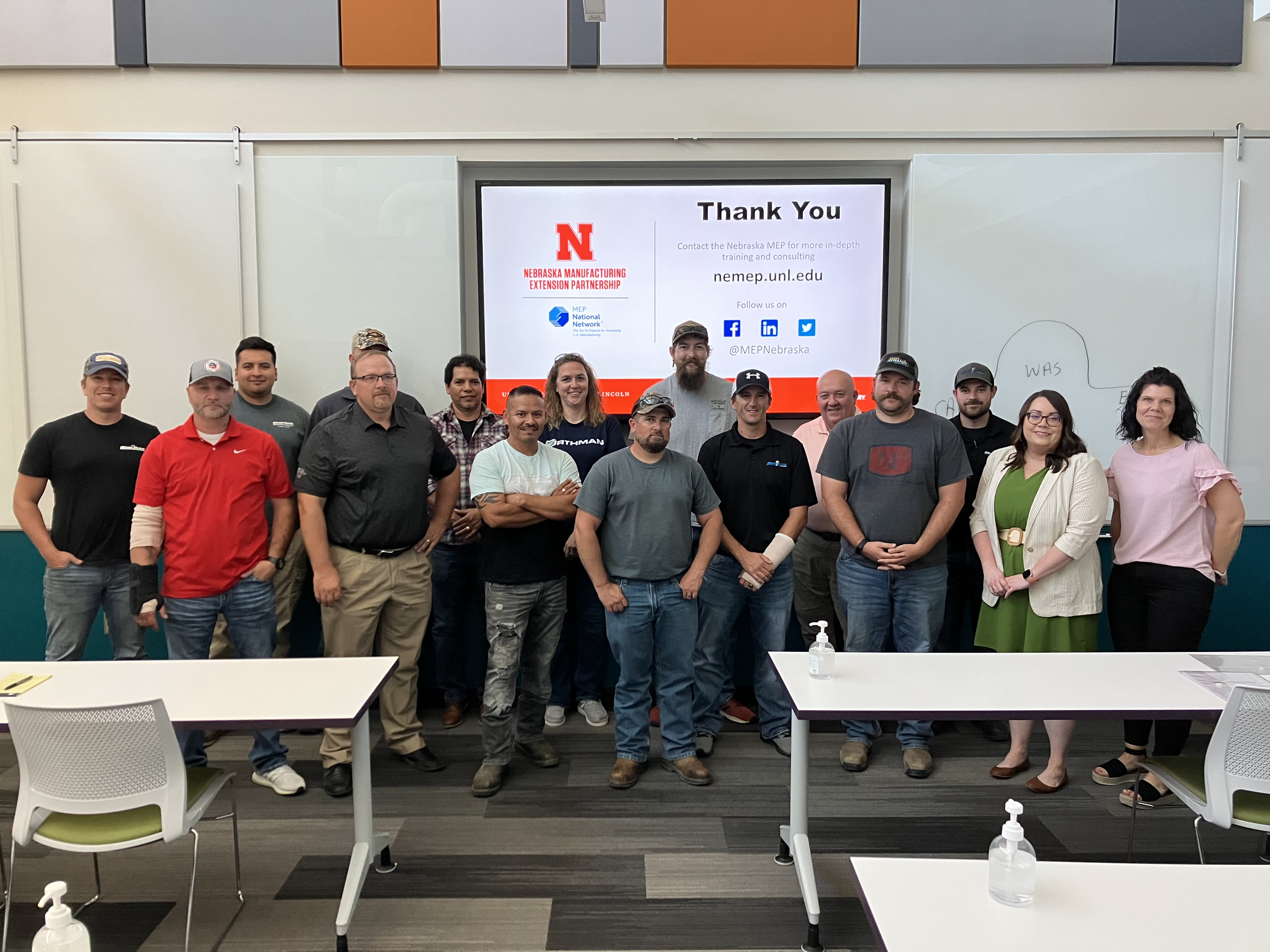
Keeping your top performing supervisors and leads is critically important, especially when it is difficult finding qualified employees. The Nebraska MEP has 3 Supervisor Development workshops that give your supervisors tools that they can use everyday to improve employee interactions, train others, and improve the production process. Each 1-day workshop is $250 per participant, which includes lunch and course materials.
Job Instruction (JI) training is designed to develop stability of your processes (standard work). This program teaches the method to instruct an operator how to perform a job correctly, safely and conscientiously. As is frequently the case, most processes are performed by various workers using different methods. Job Instruction training requires you identify the “one best way,” teach the process to this one way, and create a standard method. Doing the same thing the same way across operators and shifts creates stability. By utilizing Job Instruction, you gain the benefits of consistent training and also develop a stable process to apply continuous improvement.
Job Relations (JR) teaches how positive employee relations can be use as the foundation to your employee relationships. Participants learn how to judge good situations, develop and maintain good relations with your employees. They also learn how to recognize problem situations, how to handle them, and how to prevent them from occurring. By exchanging experiences and practicing the method during the training, supervisors practice making the right choice to take action and to follow up. This aims to strengthen their relationship with the employees.
Job Methods (JM) focuses on your continuous improvement program by building on the skills of the operators and first line leaders (team leaders, supervisors, group leaders). The aim of the program is to produce greater quantities of quality products in less time by making the best use of the people, machines and material currently available. Participants are taught how to break down jobs into their constituent operations. Every detail is questioned in a systematic manner to generate ideas for improvement. New methods are developed by eliminating, combining, rearranging, and simplifying steps in the process.
Upcoming workshop schedule:
Job Instruction, Oct 18, Central Community College, Lexington NE
Job Relations, Oct 20, Nebraska MEP, Lincoln
Job Instruction, Nov 10, the Nebraska MEP, Lincoln
Job Methods, December 8, Nebraska MEP, Lincoln
Details and Registration: https://nemep.unl.edu/workshops-events