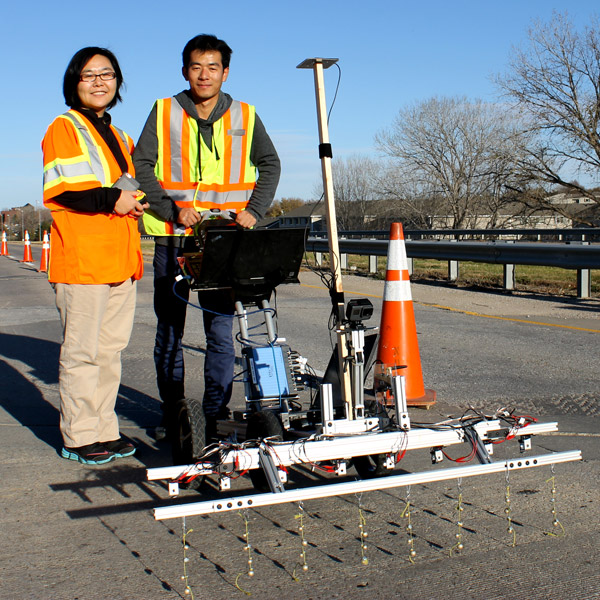
The process of testing a bridge for structural damage is long, tedious, and important for the health of the bridge and driver safety. Traditionally, road workers drag chains across the surface of a bridge to test for delamination, the separation of surface concrete from the underlying layers which can cause cracks and flaking on the driving surface. When the chains hit an area where delamination is occurring, the area produces a hollow sound, and the area is marked by a worker for repair.
Dr. Jingying Zhu is hoping to speed up this process using a rolling cart rigged with metal beads and microphones.
“Chain dragging usually takes several crews three or four hours for a two-lane bridge, including testing and defect mapping,” said Zhu. “On this cart, each string of beads is dragged along the ground as the cart is pushed and the sounds produced are recorded by an array of microphones. Because the cart with multiple microphones covers more area with better spatial resolution than the traditional chains, this system can test an entire bridge in just a few minutes. That means less lane closures to inspect bridges.”
The sounds produced by the metal beads are then analyzed to see which areas of the bridge are suffering from delamination. The sounds can then be mapped to the bridge with GPS coordinates and road workers can repair the area.
In addition to the time issues, Zhu is also looking to eliminate the possibility of human error. Chain dragging relies on a worker’s hearing and judgement. Weather, background noise, and other factors limit the effectiveness of chain dragging techniques. Zhu hopes her system will provide a consistent assessment of concrete delamination.
She believes that the metal beads will perform better than the traditional chains.
“The bead system is ironically easier to test in the field than in the lab,” said Zhu. “The grooves of a bridge surface allow the beads to jump and hit the pavement multiple times, unlike the smooth concrete slabs in the lab. This bouncing is similar to hitting the concrete with a small hammer, which gives us a more accurate analysis than the dragging of a chain.”
While it’s still in the early stages of development, Dr. Zhu is hopeful that her invention will revolutionize bridge testing.
“The goal is to one day put this system on the back of a vehicle and test an entire lane of a bridge in one pass,” said Zhu. “It will save a lot of resources.”
Dr. Zhu’s research is funded by the Nebraska Department of Roads.